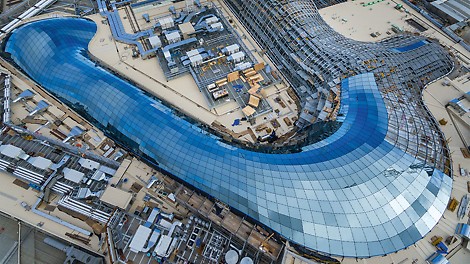
##press.media.headline##
Construction work for the 34,000 m² expansion of the Chadstone Shopping Center began back in 2014; today, the largest shopping centre in Australia has a total area of around 212,000 m². The structure receives up to 70,000 visitors a day – who now have the opportunity to stroll under an impressive, undulating curved glass roof. All work had to be carried out not only within a very tight time schedule but also while the shopping centre was open for business to the general public. This was one of the reasons why available crane capacity was severely limited which was also a factor that had to be taken into account for the work required on the enormous scaffold construction. In addition, as it was not possible to re-arrange the opening date for the expanded retail area, the resulting project schedule was extremely tight.
High flexibility for a sophisticated design
PERI engineers developed a project-specific solution in close collaboration with scaffolding contractor, Nomad Scaffolding, which was optimally adapted to match the extraordinary geometry and scaffolding heights of up to 20 m. It was necessary to be able to reach every angle of the steel construction along with bridging large areas and ensuring the reliable transfer in part of concentrated loads. Nonetheless, the scaffolding construction could be erected almost exclusively with system components.
PERI UP Flex impressively demonstrated its adaptability during this challenging project. Thanks to the modular scaffold´s high level of flexibility, the loads generated by the steel roof construction could then be reliably transferred from all areas and, in addition, the PERI UP solution offered access points to all areas of the complex shaped steel roof as well as the safe and level work spaces. The modular scaffolding can be optimally adapted to suit almost any local conditions due to the continuous metric system grid of all components along with the possibility of changing the direction of the decking. Through the self-locking ledger connection on the rosette and integrated lock against lifting, PERI UP Flex can also be installed extremely quickly.
“Lightweight“ solution for a difficult task
A particular advantage of the PERI UP Flex Modular Scaffolding in the project was the low weight of the individual system components. One reason: due to the rectangular ledger cross-section, PERI UP achieves an increased load-bearing capacity together with a corresponding reduction in weight. As a result, all components can be moved by hand and transported to the place of use. In the process, crane waiting times in particular could be prevented so that there was no resulting stoppage time in spite of the reduced crane availability. This meant that the entire construction could be dismantled without a crane as well as maintaining the tight schedule.
Safety within the system
Through the almost exclusive use of system components and well thought-out PERI UP connection technology by means of rosette nodes, time-consuming tube-and-coupler operations could be consistently avoided during scaffold assembly. In addition, thanks to the different part lengths from 25 cm, all working areas could be fully covered with PERI UP Flex featuring a complete absence of any gaps while obstacles and rising steel profiles could easily be accommodated and covered virtually gap-free. For users of the scaffolding, this meant that all working areas could be safely reached without any dangerous tripping hazards. During use, end-to-end guardrails and yellow toe boards as well as non-slip decking ensured a high level of operational safety. This allowed safe and cost-effective working operations at heights of up to 20 m above the ground on work platforms up to 85 m long.
The target deadline for all working operations was safely and reliably achieved: three days before the opening date, the scaffolding team dismantled the last PERI UP system components.