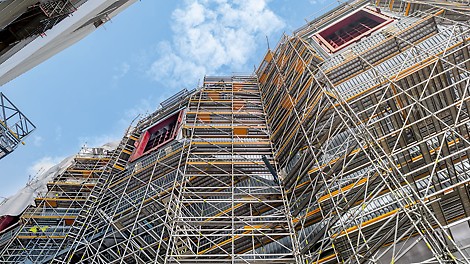
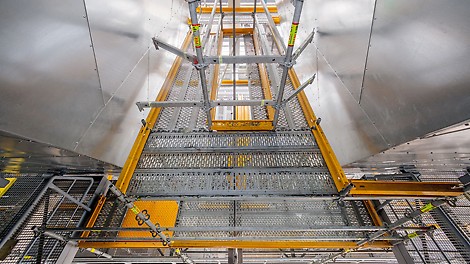
##press.download.headline##
##press.media.headline##
The 1,600-MW Eemshaven power plant in the Dutch province of Groningen is a highly efficient coal-fired power station complete with a switchable biomass combustion facility, and is equipped with the latest cleaning and filter technology. The direct coastal location on the North Sea, and the close proximity to a port, provide ideal conditions for the supply of cooling water as well as required quantities of fuel. Eemshaven is deemed an important component regarding the country´s energy supply due to its flexible and weather-independent production of electricity, especially in combination with the utilisation of wind and solar energy. The installation is scheduled to commence operations in 2014 after a 4-year long construction period.
Safe working conditions
The two electric filters for flue gas desulphurisation are 64 m long and 35 m high respectively. For safely executed welding and insulation work in accordance with the highest quality standards, working platforms and access means were provided on the basis of the Peri Up Rosett Flex modular scaffolding system. An externally-fitted working scaffold with integrated 75-cm flights of stairs was used for the final assembly of altogether eight inlet ducts. The scaffold solution could be optimally adjusted through its metric grid arrangement to suit the up to 4.50 m cantilevered funnel shape – in part, suspended from a gallows structure comprised of Peri Up system components.
Assembly of the modular scaffolding for the 35 m high working scaffold was carried out extremely safely using the guardrail in advance thus making rope protection unnecessary. In addition, the Peri scaffolding solution took into account the existing steel structure as well as those walkways already mounted, and was easily adapted to the structural conditions.
Spatial adjustment
Using the Peri Up grid system is a great advantage especially for the spatial scaffolding assembly of the filter funnels: scaffolding on the existing steel structure can easily be modified – for optimum adaptation to the plant components on which work is to be carried out, without requiring the assembly of a time-consuming tube-and-coupler construction. For this, the scaffold bays can be divided horizontally and vertically as required with the help of standard components. As a result, the bay lengths of the lower sections are generously dimensioned thus ensuring easy accessibility and with a minimal use of materials. In the area of the structural elements that are to be worked on – and which require geometrical adjustments – 300 cm scaffold bays, for example, are divided into three sections with 75 cm, 150 cm and 75 cm widths so that construction work can continue upwards with reduced bay widths.
High level of safety in industrial construction
As a rule, industrial buildings and installations fulfil functional and economic requirements. This also includes the construction of power plants for the generation of electricity as well as their expansion, maintenance and modernization. Planning and execution comply with the requirements of existing and future production processes – often associated with strict safety regulations. Furthermore, at the same time, completing the planned shell construction work and realising all technical equipment requirements require close coordination of the construction progress throughout.
Here, in addition to execution drawings and proof of stability, Peri supports its customers with required approvals, type tests as well as assembly instructions. Approvals provide – as a result of consistent implementation of a quality management system – the necessary legal basis for the use of scaffolding. Moreover, system-related assembly instructions contain all the information and details that are required for fast and safe installation. Due to its worldwide operations, Peri provides a comprehensive range of technical documentation in many languages.