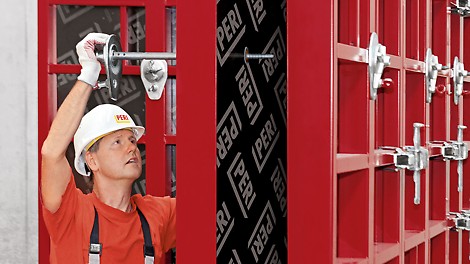
##press.download.headline##
##press.media.headline##
The focus of PERI developments has always been on the highest possible rationalization of the work involved in formwork and scaffolding applications – whilst simultaneously providing safe working conditions for the users. The reliable top quality and the associated long service life of PERI products has also led to a continuous development of systems that are often in use over several decades. In Munich, the Weissenhorn-based provider presented a range of innovations, further developments and new system enhancements.
With a visitor-oriented stand concept, PERI moved its live presentations of both the new and proven systems even further under the spotlight. On a large market square in the centre of the stand, wall and slab formwork as well as scaffolding were constantly in operation. Thus, visitors had the opportunity to look at the system details and to convince themselves of their functionality at first hand. Also in the other exhibition areas, there were "hands-on" PERI systems – in order to test the handling, having the system applications explained in detail as well as discussions with PERI experts and colleagues. Apart from the complex formwork and scaffolding systems, the exhibition also featured numerous accessories and diverse construction site equipment. Often overlooked, these PERI products provide clever solutions with high quality which result in faster daily working operations on the jobsite. New manufacturing methods along with other materials also lead to new products – at the bauma, for example, the first plastic stopend angle for reduced loads on the structure was presented.
However, PERI services go far beyond just the development and manufacture of formwork and scaffolding systems. The company is much more of a solution provider with a comprehensive range of services and ensuring the best possible user support throughout all phases of a project. At the bauma, PERI´s unparalleled range of services certainly lived up to expectations through numerous impressive presentations of these and exemplary project solutions. PERI specialists provided visitors to the stand with valuable insights into the operational processes and performance details, and were ready throughout to answer all questions posed about the systems and their applications. A substantial area was dedicated to exhibiting those services dealing with the whole construction process. Among other things, PERI demonstrated how the economic efficiency could be further increased during the execution of the construction work through technical processing as well as 3D planning and realistic visualizations. In addition, the specialists presented other services in the PERI portfolio along with the added value these have for daily jobsite operations: from formwork assembly and the rental, assembly and repair service, though to comprehensive project support on the construction site, PERI provides valuable support during all phases of the execution. Unveiled for the first time to an international audience was the myPERI online portal which offers PERI customers access to a comprehensive database of technical product information as well as specific project data of PERI construction sites around the clock.
Wall and Slab Formwork expanded for new applications, Fall Protection supplemented
For wall and slab formwork systems, PERI relies on proven systems that make a very convincing case through their outstanding working time requirement values. Systems that have established themselves in the industry during recent years are now even more versatile and flexible with the addition of new system components. For ensuring safer working areas, PERI has further enhanced the PROKIT safety system for applications on open building edges and on the formwork.
More possibilities with MAXIMO
For the wall formwork, the MAXIMO panel formwork was the focus of attention. In 2007, with the development of the MX tie technology – with ties installed on only one side – PERI set a new benchmark in the industry and the system is even more versatile than ever before. Then, the continuous further development in order to meet diverse user requirements continues. Existing improvement potential was identified and used to further optimize the system.
In Munich, PERI presented the new MAXIMO MX 18 tie with a permissible load capacity of 120 kN. For using this stronger MX 18 tie together with the wingnut MX 18, only the MX 18 removable sealing has to be mounted in the panel formwork. By means of a special tool, the newly developed removable sealing can be quickly replaced during operations on the jobsite – and in case of damage, can also be changed without any problems. With the MX 18 tie, MAXIMO can accommodate a higher fresh concrete pressure and can now be used for wall thickness up to 60 cm. For project-specific planning, even a concrete pressure clearly in excess of 80 kN /m² is feasible in the system with the MAXIMO formwork and MX 18 tie technology. A new tension and compression brace is also available for walls up to 100 cm thick. This example shows how an existing formwork system can be extended by means of a few supplementary components for additional tasks without requiring any large investment. This is particularly advantageous for infrequent applications, e.g. for such a high fresh concrete pressure.
Significant simplification regarding the installation of safe working areas is provided by the new MXK bracket. Apart from the bracket itself, the core components of the pre-assembled platform system are the MXK plastic scaffolding deck, MXK guardrail posts and the MXK side mesh barrier. The main features are the few, very lightweight system components and the well thought-out system solutions also for corner and filler sections. As an alternative to the plastic decking, conventional linings can be fixed to the brackets. As anti-fall protection, proven 1.10 m side mesh barriers are used taken from the PROKIT system which are available in conveniently-sized lengths of 240 cm, 120 cm and 90 cm. The entire working platform is completely pre-assembled on the ground and used on MAXIMO and TRIO panel formwork.
Lightweight DOMINO and LIWA wall formwork systems also expanded
The lighter wall formwork systems have also been supplemented with new system components. DOMINO, as lightweight panel formwork for building construction and civil engineering, now allows more applications in the system through the additional panel height of 150 cm – for example, sleeve foundations and parapets or swimming pools. An additional panel width of 35 cm for more flexibility and the stable internal corner made of steel for accurate 90° corners ensure that numerous daily tasks on the construction site can be carried out much quicker.
Launched at bauma 2010, the LIWA wall formwork can be moved crane-independently and consists of only four different panel widths and one corner panel that can form virtually all ground plans as well as beams. The LIWA range was extended with the addition of an aluminium a corner panel, a stabile wedge clamp for standard panel connections and a push-pull prop connection for connecting vertically and horizontally.
Change of direction for SKYDECK slab formwork
SKYDECK slab formwork with the lightweight individual aluminum panels has been convincing countless users for many years with its systematic assembly sequence and particularly short shuttering times. Improvements have now been made to the anti-fall protection on the slab edges: the complete guardrail unit with all safety-relevant features can be installed without tools in any position on the longitudinal beams. Once locked in position, it provides safe and reliable protection. The guardrails are available in widths of 150 cm and 75 cm, and rounded off with suitable stacking devices for transportation.
In addition, new prop heads expand the flexibility of the SKYDECK slab formwork whereby a change in direction of the longitudinal beams at right angles is possible. By turning the SKYDECK panels 90°, infill areas are minimized even further and allows the system to be optimally adapted to accommodate non-rectangular ground plans. This results in time and cost-savings for the user as no compensations have to be created between two formwork assemblies with different panel directions. The new prop head is available in two versions, for providing direct support as well as execution with the drophead.
VARIODECK complemented with new accessories
For the large-sized slab table with a forming area up to 18 m², PERI has optimized the equipment used for moving. The table lift and transportation fork have now been adapted for table lengths of 6.00 m. Also presented during the fair was a system-integrated edge beam solution with only two additional system components which can be used for beams up to 60 cm high and 30 cm wide. The striking procedure is extremely fast: only the props that are positioned under the beam need to be spindled.
The PROKIT safety system
For the reliable securing of edges on building shells, PERI presented the first components of the PROKIT safety system at bauma 2010, further additions followed at this year's show.
This included different fastening means. For attaching the feet for the PROKIT posts on the concrete slab, special screw-in sleeves were developed. Thanks to the coarse external thread, these can be screwed into the fresh concrete by hand requiring only two turns. After the concrete has set, a standard M16 bolt can be screwed into the internal thread. The slab foot can thus be mounted without any subsequent drilling in the hardened concrete and the PROKIT posts can then be easily and safely installed. And with the new PSC sheet piling clamp, the PROKIT side mesh barriers can now also be mounted on sheet piling and Berlin-type pit linings. Fixing with a triple wingnut can be carried out from the top, below and from both sides. The clamp and posts can also be installed in a rotated position.
Likewise presented were the new EP 110 pallets for transportation and storage of up to 25 PROKIT side mesh barriers. Here, the barriers are placed in an upright position so that they can be removed ergonomically. The EP 110 pallets can be enclosed with a frame and are stackable.
PERI Slab Props and Shoring
PERI provides solutions to meet all requirements for shoring systems, from simple slab props through to spatial load-bearing scaffolds – and always compatible with PERI slab formwork systems. Here, too, further potential for improvement was fully exploited – for example, improving the ergonomics and safety, increasing the load-bearing capacity as well as the development of new areas of application.
PEP Ergo: tubular steel props with maximum load-bearing capacity and practical details
The PEP Ergo range of props has been supplemented by five additional tubular steel props. This includes the PEP Ergo E-300 and PEP Ergo E-400 which feature an unprecedented load-bearing capacity for tubular steel slab props of up to 50 kN. The props are characterized by their low self-weight and through numerous, intelligent detailed solutions. For example, the easy loosening of the nut through the innovative G-hook, a large adjustment range of 12 cm, the integrated safety clearance, the triple-winged nut with hardened bearing surface and the stamped measuring tape. In total, the product group´s nine props now optimally cover the complete range of applications for daily construction site operations with a minimum of different prop types.
PERI UP Rosett Flex heavy-duty props: the new heavy-duty prop comprised of lightweight system components with hydraulic lowering and prestressing
The system components of the PERI UP Rosett Flex modular scaffolding can now also be used for heavy-duty props. The middle section of the 4-leg suppport consists of standard system components of the modular scaffold. New components are head and lowering spindles as well as a connecting plate. The TR head spindle has an adjustment range of 55 cm while the HD lowering spindle is used as a base spindle and serves as a housing for the lifting cylinder of the hydraulic unit. The UJC connecting plate transfers the forces from the prop into the lowering spindle. The dedicated HD hydraulic unit allows a stroke length of 68 mm.
The heavy-duty prop is used for the safe transfer of concentrated loads of up to 200 kN. These loads occur in shoring as well as for building redevelopment. The hydraulic cylinder in the base allows the deformation-controlled lowering of the props in 10-mm increments and the torque-controlled lowering of props under load by reading off in kN on the manometer. Likewise, the hydraulic allows the systematic, torque-controlled pre-tensioning of the prop up to 200 kN which is required for shoring in reconstruction projects. All components can be transported by hand, and using standard system components to the greatest possible extent makes the solution extremely cost-effective.
PERI UP Rosett Flex: the MDS shoring tower with integrated safety
On the basis of the PERI UP shoring system and supplemented by a few additional components, the specialists from Weissenhorn have developed a shoring tower which provides a very high level of safety during assembly and dismantling. For assembling the MDS shoring tower, scaffolders work whilst standing in a safe position in the centre of the tower with the help of a newly developed platform. This platform is the key element during the assembly because it accelerates the handling while at the same time providing delivering a high degree of safety as all levels of the shoring tower are assembled and dismantled with protection automatically provided by a guardrail in advance. The MDS shoring tower can only be extended upwards if the leading platform has been suspended on the next higher-positioned ledger. As a result, the scaffolder is secure during every stage of the assembly without requiring any additional anti-fall equipment. In addition, the supply of materials is carried out safely inside the tower.
The PERI UP Rosett Flex MDS shoring tower is used in "classic" shoring operations with leg loads of up to 50 kN. In the direction of the frame, the width is 125 cm; in the longitudinal direction, the dimensions can be freely selected in accordance with the static and geometrical requirements. Furthermore, all other system components of the PERI UP Rosett Flex modular scaffolding can also be used.
PERI Climbing Technology
For the area of PERI climbing technology, PERI presented several new systems that have been successfully proven at various jobsites in the past few months. This also includes the ACS C 200, the self-climbing system for high-rise building cores with generously-sized platforms and high load-bearing capacities with fast cycle times. In addition, safety has been further optimized so that all-round fall protection is now possible on PERI climbing systems with just a minimum number of new system components.
SCS: the new climbing system for single-sided forming
At bauma 2013, PERI presented for the new SCS climbing formwork (SCS = Single-Sided Climbing System) for the first time to a wide professional public. Since summer 2011, more than 6,000 of these brackets have been in use for the expansion of the Panama Canal. With the robust and flexible bracket system, the loads from the fresh concrete pressure are transferred without formwork ties via the bracket into the climbing anchors.Typical areas of application include dams, locks, cooling towers, bunkers and vaults, pier heads and tunnels.
The new climbing system SCS is characterized by its high level of cost-effectiveness because, thanks to the modular design concept with its multi-part brackets, it can be optimally adapted to the respective requirements and building geometries. Moreover, the high load-bearing capacity of the brackets together with high utilization grade of the certified anchoring makes the new system more efficient than the SKS bracket it has replaced. For the starter and for all subsequent standard cycles, the same formwork and the same system components are used. In order to be able to work safely on forward and reverse-inclined structures, the finishing and concreting platforms can be tilted by 15° and 30°, whilst the working platform can be adjusted continuously. As a result, it is always be aligned horizontally thus providing a safe working environment.
PERI presented the system in two versions. The SCS 190 bracket is available as a low-cost option that requires very little space. For striking, the formwork is simply tilted. With the SCS 250, the formwork can be retracted by more than 60 cm by means of a carriage. This provides sufficient space for all formworking and reinforcement operations.
LPS Screen: the lightweight climbing protection panel
PERI developed the new LPS Screen (LPS = Light Protection System) climbing protection panel as a weight-optimized alternative to the conventional, closed enclosures. The rail-mounted protection panel with rentable mesh panels as the enclosure can be used extremely flexibly and is easily adapted to suit complex building forms thanks to the telescopic function. The close-meshed panels serve as a wind deflector as well as providing anti-fall protection during assembly of the top slab formwork. One particular advantage during striking of the respective floors is that the light-transmissive structure of the mesh panels allows working operations to be carried out in daylight. In addition, the panels are very light which simplifies installation and the climbing procedure whilst also reducing the load on the building itself. The meshed enclosure is quickly and easily mounted to the LPS climbing rails by means of clamp connectors – a crane is not required. Continuous connections are possible thus allowing a free arrangement of the climbing rails.
The slab shoe-guided climbing rails facilitate a fast and safe moving procedure. As an option, mobile hydraulic climbing devices also allow crane-independent moving.
PERI offers the LPS Screen in two versions. On the one hand, straight and continuous and, on the other, with a working platform that provides access to the stopend formwork.
The mesh panels can also be used with RCS climbing rails whereby they are simply clamped to the climbing rail with the same LPS clamp adapters. With this lightweight and completely rentable solution, the proven PERI RCS P climbing protection panel is even more cost-effective.
The RCS MP Landing Platform: fast moving procedure with flexible landing platforms
For moving formwork and construction materials in high-rise buildings, PERI presented the RCS MP landing platform at bauma 2013. Optionally, the new system can be either anchored in the slab or simply clamped in position between two storey slabs by means of MULTIPROP props. The RCS MP landing platform is supplemented through the checker plate decking and LPS mesh enclosure. The solution is completely rentable and is delivered already pre-assembled. The platform has a cantilever of 3.75 m and serves to move the SKYDECK and building materials whereby the 5.50 m cantilevered platform is used for moving large-sized slab tables. With the larger version, post tensioning is integrated in the side protection which minimizes the amount of deflection on the platform.
PERI Civil Engineering Technology
For tunnel and bridge construction, a number of new systems have been developed over the past three years which have already impressively proved themselves during tough jobsite conditions. Shortly after being showcased at the last bauma, the VARIOKIT heavy-duty shoring tower, for example, was successfully used in summer 2010 as shoring for bridge construction as well as for supporting extremely heavy precast concrete elements. And the new VARIOKIT balanced cantilever equipment was used for the first time in spring 2011 in Poland for the construction of a bridge over the River Dunajec.
PERI presented all of the new solutions in April 2013 in the Civil Engineering Technology area of the stand with a number of exhibits, but also especially through demonstrations and competent presentations of solutions by the PERI team of experts. In addition, PERI also dedicated one particular area to the design and realization of complex forms. PERI´s special expertise ranges from planning and cutting-to-size through to the creation of 3D formwork units which can be assembled on the construction site similar to a system formwork.
The VARIOKIT heavy-duty truss girder
PERI has clearly expanded the application possibilities of the VARIOKIT engineering construction kit. With new VARIOKIT system components, it is now possible to also create a heavy-duty truss girder – as a suitable further development to supplement the VARIOKIT heavy-duty shoring tower. During the development, PERI took into account the load-bearing capacity of the tower as well as the challenging requirements of everyday construction work. At bauma 2013, the heavy-duty truss girder was impressively presented having been positioned under a bridge with original dimensions.
The modular lattice system can be used for spans up to 40 m and is characterized by a very high load-bearing capacity. With the continuously adjustable telescopic support frame, all spans can be realized with centimetre precision. In addition, the calotte bearing allows easy adaption to the longitudinal and lateral inclinations of the superstructure. The heavy-duty truss girder can be quickly assembled by means of fitting pins.
The compatibility with the VARIOKIT heavy-duty shoring tower through the VRB main beam, facilitates optimized solutions in the heavy-duty shoring sector, whilst the optional PERI UP scaffolding in the bottom section provides completely safe working conditions.
The VARIOKIT balanced cantilever equipment
The VARIOKIT construction kit has been used very successfully in recent months also for bridge structures with different superstructure cross-sections. With new components for the longitudinal direction of the balanced cantilever equipment, up to 5.75 m long segments can be concreted. In the transverse direction, existing system components are used. Thus, PERI achieves a maximum level of adaptability for a wide range of bridge sections. Furthermore, the moving procedure to the next concreting section is now extremely practice-oriented. Then, thanks to a newly developed mechanical solution, the required manual work is quickly carried out.
As all system components, with the exception of the tie technology, are available in the PERI rental parks, the balanced cantilever unit is also extremely cost-effective with VARIOKIT. All modules incidentally can be re-used for future projects without requiring any further adaptation – the majority even for other types of civil engineering structures.
The new VGK-2 parapet bracket
For shuttering of bridge cantilevered parapets and for their refurbishment, PERI presented new parapet brackets. These are characterized by a low individual component weight of a maximum 22 kg and a high degree of flexibility for adapting to different parapet geometries. Because the brackets can be mounted and aligned while positioned on the platform, this improves work safety. The completely enclosed decking, side protection as well as anchoring with general building inspectorate approval guarantees safe utilization. The bracket makes a very convincing and impressive case during refurbishment work: firstly, as a working area for dismantling operations and subsequently as the basis for the formwork of the new cantilevered parapet.
PERI UP Scaffold Technology
PERI presented a wide range of scaffolding solutions and applications through numerous demonstrations on the market square area and a number of dedicated demonstration areas. Safer and faster assembly and dismantling along with access means for different requirements was the main focus throughout. New system components were presented for use in industry and also for the weather protection roof LGS.
New: the PERI UP Trolley UFS 20
This newly-developed trolley serves to create rollable suspended scaffolding on steel girders. It is intended for hanging scaffolds which are mounted, for example, on the underside of oil platforms or for bridges on I-shaped steel profiles. The trolley is suitable for flange widths from 200 mm to 320 mm and flange thicknesses up to approx. 40 mm. The rollers are bearing-mounted and allow connections to inclined girders up to an angle of 15°.
The system spacings of the scaffold are retained during use of the UFS 20 trolley in spite of variable distances between the steel girders: as the position of the standards vis-á-vis the girder axis can be continuously adjusted up to 125 mm, this always results in system dimensions in 25 cm increments for the scaffold sub-structure.
Improved working safety with the weather protection roof LGS
The LGS lattice girder system has established itself as a reliable and easy-to-use lightweight weather protection roof – supplemented by components for the support and ridge formation. For closing the frame construction with sheeting, PERI has now developed a considerably faster solution. In addition, the new brackets ensure that working conditions on the roof are much safer.
Closing the construction with sheeting is now much easier and faster because the optimized Keder tracks along with the new Keder couplings reduce friction and thus the amount of physical effort required. In addition, a new eave element with a curved shape allows the sheeting to be pulled more easily together and tightly closed also in the support areas of the protection roof. Another new feature is that through the integrated smooth-running mechanism, the sheeting can be evenly pulled across the complete width on rollers.Through this new solution for the installation of the sheeting, transport of the Keder sheeting is also simplified.
Furthermore, PERI has developed new system components that ensure safe access to the protection roof. Then, in order to detach prefabricated roof trusses from the crane or brace individual pre-assembled truss sections with ledgers and diagonals, access means within the construction is absolutely necessary.
The new brackets are mounted on the LGS element with 3.00 m spacings, whilst safe walkways along the truss girder are formed with proven UDI decks and standard guardrails. When working under the roof, the use of personal protection gear against falling is therefore not necessary. The pre-assembly of the brackets is carried out together with the roof segments on the ground – to a very large extent without tools. Then the complete units are lifted by crane into the required position. Access is possible through the load-carrying system and support construction.
Quickly mounted – the new ULS Flex lattice girder
Comprised of lightweight individual components, the steel ULS Flex lattice girder is primarily intended for those applications where the long length of single-piece lattice girders means installation cannot take place.
The girder consists of five lightweight individual components with a maximum length of 1.50 m and a top weight of 15.4 kg. The quick and easy assembly with pins and cotter pins – without any tube coupling connections – makes the new lattice girder extremely practical for every construction site. Due to its compact dimensions and low individual weights, the ULS Flex system parts fit through narrow manholes and small freight elevators - an important aspect, for example, during renovation work in old buildings. The easy to handle elements facilitate optimum adaptation in increments of 25 cm for bridging lengths from 3.00 m to 9.00 m.
At this year´s bauma, PERI presented a number of new formwork and scaffolding systems as well as a wide range of further developments. On an area of over 4,000 m², the exhibition offered visitors the opportunity to learn more about proven and innovative technology at first hand. In addition to the numerous live demonstrations, the huge numbers of visitors to the stand – from home and abroad – were able to take part in detailed technical discussions with PERI specialists, along with finding out more about the extensive PERI services portfolio.
The focus of PERI developments has always been on the highest possible rationalization of the work involved in formwork and scaffolding applications – whilst simultaneously providing safe working conditions for the users. The reliable top quality and the associated long service life of PERI products has also led to a continuous development of systems that are often in use over several decades. In Munich, the Weissenhorn-based provider presented a range of innovations, further developments and new system enhancements.
With a visitor-oriented stand concept, PERI moved its live presentations of both the new and proven systems even further under the spotlight. On a large market square in the centre of the stand, wall and slab formwork as well as scaffolding were constantly in operation. Thus, visitors had the opportunity to look at the system details and to convince themselves of their functionality at first hand. Also in the other exhibition areas, there were "hands-on" PERI systems – in order to test the handling, having the system applications explained in detail as well as discussions with PERI experts and colleagues. Apart from the complex formwork and scaffolding systems, the exhibition also featured numerous accessories and diverse construction site equipment. Often overlooked, these PERI products provide clever solutions with high quality which result in faster daily working operations on the jobsite. New manufacturing methods along with other materials also lead to new products – at the bauma, for example, the first plastic stopend angle for reduced loads on the structure was presented.
However, PERI services go far beyond just the development and manufacture of formwork and scaffolding systems. The company is much more of a solution provider with a comprehensive range of services and ensuring the best possible user support throughout all phases of a project. At the bauma, PERI´s unparalleled range of services certainly lived up to expectations through numerous impressive presentations of these and exemplary project solutions. PERI specialists provided visitors to the stand with valuable insights into the operational processes and performance details, and were ready throughout to answer all questions posed about the systems and their applications. A substantial area was dedicated to exhibiting those services dealing with the whole construction process. Among other things, PERI demonstrated how the economic efficiency could be further increased during the execution of the construction work through technical processing as well as 3D planning and realistic visualizations. In addition, the specialists presented other services in the PERI portfolio along with the added value these have for daily jobsite operations: from formwork assembly and the rental, assembly and repair service, though to comprehensive project support on the construction site, PERI provides valuable support during all phases of the execution. Unveiled for the first time to an international audience was the myPERI online portal which offers PERI customers access to a comprehensive database of technical product information as well as specific project data of PERI construction sites around the clock.
Wall and Slab Formwork expanded for new applications, Fall Protection supplemented
For wall and slab formwork systems, PERI relies on proven systems that make a very convincing case through their outstanding working time requirement values. Systems that have established themselves in the industry during recent years are now even more versatile and flexible with the addition of new system components. For ensuring safer working areas, PERI has further enhanced the PROKIT safety system for applications on open building edges and on the formwork.
More possibilities with MAXIMO
For the wall formwork, the MAXIMO panel formwork was the focus of attention. In 2007, with the development of the MX tie technology – with ties installed on only one side – PERI set a new benchmark in the industry and the system is even more versatile than ever before. Then, the continuous further development in order to meet diverse user requirements continues. Existing improvement potential was identified and used to further optimize the system.
In Munich, PERI presented the new MAXIMO MX 18 tie with a permissible load capacity of 120 kN. For using this stronger MX 18 tie together with the wingnut MX 18, only the MX 18 removable sealing has to be mounted in the panel formwork. By means of a special tool, the newly developed removable sealing can be quickly replaced during operations on the jobsite – and in case of damage, can also be changed without any problems. With the MX 18 tie, MAXIMO can accommodate a higher fresh concrete pressure and can now be used for wall thickness up to 60 cm. For project-specific planning, even a concrete pressure clearly in excess of 80 kN /m² is feasible in the system with the MAXIMO formwork and MX 18 tie technology. A new tension and compression brace is also available for walls up to 100 cm thick. This example shows how an existing formwork system can be extended by means of a few supplementary components for additional tasks without requiring any large investment. This is particularly advantageous for infrequent applications, e.g. for such a high fresh concrete pressure.
Significant simplification regarding the installation of safe working areas is provided by the new MXK bracket. Apart from the bracket itself, the core components of the pre-assembled platform system are the MXK plastic scaffolding deck, MXK guardrail posts and the MXK side mesh barrier. The main features are the few, very lightweight system components and the well thought-out system solutions also for corner and filler sections. As an alternative to the plastic decking, conventional linings can be fixed to the brackets. As anti-fall protection, proven 1.10 m side mesh barriers are used taken from the PROKIT system which are available in conveniently-sized lengths of 240 cm, 120 cm and 90 cm. The entire working platform is completely pre-assembled on the ground and used on MAXIMO and TRIO panel formwork.
Lightweight DOMINO and LIWA wall formwork systems also expanded
The lighter wall formwork systems have also been supplemented with new system components. DOMINO, as lightweight panel formwork for building construction and civil engineering, now allows more applications in the system through the additional panel height of 150 cm – for example, sleeve foundations and parapets or swimming pools. An additional panel width of 35 cm for more flexibility and the stable internal corner made of steel for accurate 90° corners ensure that numerous daily tasks on the construction site can be carried out much quicker.
Launched at bauma 2010, the LIWA wall formwork can be moved crane-independently and consists of only four different panel widths and one corner panel that can form virtually all ground plans as well as beams. The LIWA range was extended with the addition of an aluminium a corner panel, a stabile wedge clamp for standard panel connections and a push-pull prop connection for connecting vertically and horizontally.
Change of direction for SKYDECK slab formwork
SKYDECK slab formwork with the lightweight individual aluminum panels has been convincing countless users for many years with its systematic assembly sequence and particularly short shuttering times. Improvements have now been made to the anti-fall protection on the slab edges: the complete guardrail unit with all safety-relevant features can be installed without tools in any position on the longitudinal beams. Once locked in position, it provides safe and reliable protection. The guardrails are available in widths of 150 cm and 75 cm, and rounded off with suitable stacking devices for transportation.
In addition, new prop heads expand the flexibility of the SKYDECK slab formwork whereby a change in direction of the longitudinal beams at right angles is possible. By turning the SKYDECK panels 90°, infill areas are minimized even further and allows the system to be optimally adapted to accommodate non-rectangular ground plans. This results in time and cost-savings for the user as no compensations have to be created between two formwork assemblies with different panel directions. The new prop head is available in two versions, for providing direct support as well as execution with the drophead.
VARIODECK complemented with new accessories
For the large-sized slab table with a forming area up to 18 m², PERI has optimized the equipment used for moving. The table lift and transportation fork have now been adapted for table lengths of 6.00 m. Also presented during the fair was a system-integrated edge beam solution with only two additional system components which can be used for beams up to 60 cm high and 30 cm wide. The striking procedure is extremely fast: only the props that are positioned under the beam need to be spindled.
The PROKIT safety system
For the reliable securing of edges on building shells, PERI presented the first components of the PROKIT safety system at bauma 2010, further additions followed at this year's show.
This included different fastening means. For attaching the feet for the PROKIT posts on the concrete slab, special screw-in sleeves were developed. Thanks to the coarse external thread, these can be screwed into the fresh concrete by hand requiring only two turns. After the concrete has set, a standard M16 bolt can be screwed into the internal thread. The slab foot can thus be mounted without any subsequent drilling in the hardened concrete and the PROKIT posts can then be easily and safely installed. And with the new PSC sheet piling clamp, the PROKIT side mesh barriers can now also be mounted on sheet piling and Berlin-type pit linings. Fixing with a triple wingnut can be carried out from the top, below and from both sides. The clamp and posts can also be installed in a rotated position.
Likewise presented were the new EP 110 pallets for transportation and storage of up to 25 PROKIT side mesh barriers. Here, the barriers are placed in an upright position so that they can be removed ergonomically. The EP 110 pallets can be enclosed with a frame and are stackable.
PERI Slab Props and Shoring
PERI provides solutions to meet all requirements for shoring systems, from simple slab props through to spatial load-bearing scaffolds – and always compatible with PERI slab formwork systems. Here, too, further potential for improvement was fully exploited – for example, improving the ergonomics and safety, increasing the load-bearing capacity as well as the development of new areas of application.
PEP Ergo: tubular steel props with maximum load-bearing capacity and practical details
The PEP Ergo range of props has been supplemented by five additional tubular steel props. This includes the PEP Ergo E-300 and PEP Ergo E-400 which feature an unprecedented load-bearing capacity for tubular steel slab props of up to 50 kN. The props are characterized by their low self-weight and through numerous, intelligent detailed solutions. For example, the easy loosening of the nut through the innovative G-hook, a large adjustment range of 12 cm, the integrated safety clearance, the triple-winged nut with hardened bearing surface and the stamped measuring tape. In total, the product group´s nine props now optimally cover the complete range of applications for daily construction site operations with a minimum of different prop types.
PERI UP Rosett Flex heavy-duty props: the new heavy-duty prop comprised of lightweight system components with hydraulic lowering and prestressing
The system components of the PERI UP Rosett Flex modular scaffolding can now also be used for heavy-duty props. The middle section of the 4-leg suppport consists of standard system components of the modular scaffold. New components are head and lowering spindles as well as a connecting plate. The TR head spindle has an adjustment range of 55 cm while the HD lowering spindle is used as a base spindle and serves as a housing for the lifting cylinder of the hydraulic unit. The UJC connecting plate transfers the forces from the prop into the lowering spindle. The dedicated HD hydraulic unit allows a stroke length of 68 mm.
The heavy-duty prop is used for the safe transfer of concentrated loads of up to 200 kN. These loads occur in shoring as well as for building redevelopment. The hydraulic cylinder in the base allows the deformation-controlled lowering of the props in 10-mm increments and the torque-controlled lowering of props under load by reading off in kN on the manometer. Likewise, the hydraulic allows the systematic, torque-controlled pre-tensioning of the prop up to 200 kN which is required for shoring in reconstruction projects. All components can be transported by hand, and using standard system components to the greatest possible extent makes the solution extremely cost-effective.
PERI UP Rosett Flex: the MDS shoring tower with integrated safety
On the basis of the PERI UP shoring system and supplemented by a few additional components, the specialists from Weissenhorn have developed a shoring tower which provides a very high level of safety during assembly and dismantling. For assembling the MDS shoring tower, scaffolders work whilst standing in a safe position in the centre of the tower with the help of a newly developed platform. This platform is the key element during the assembly because it accelerates the handling while at the same time providing delivering a high degree of safety as all levels of the shoring tower are assembled and dismantled with protection automatically provided by a guardrail in advance. The MDS shoring tower can only be extended upwards if the leading platform has been suspended on the next higher-positioned ledger. As a result, the scaffolder is secure during every stage of the assembly without requiring any additional anti-fall equipment. In addition, the supply of materials is carried out safely inside the tower.
The PERI UP Rosett Flex MDS shoring tower is used in "classic" shoring operations with leg loads of up to 50 kN. In the direction of the frame, the width is 125 cm; in the longitudinal direction, the dimensions can be freely selected in accordance with the static and geometrical requirements. Furthermore, all other system components of the PERI UP Rosett Flex modular scaffolding can also be used.
PERI Climbing Technology
For the area of PERI climbing technology, PERI presented several new systems that have been successfully proven at various jobsites in the past few months. This also includes the ACS C 200, the self-climbing system for high-rise building cores with generously-sized platforms and high load-bearing capacities with fast cycle times. In addition, safety has been further optimized so that all-round fall protection is now possible on PERI climbing systems with just a minimum number of new system components.
SCS: the new climbing system for single-sided forming
At bauma 2013, PERI presented for the new SCS climbing formwork (SCS = Single-Sided Climbing System) for the first time to a wide professional public. Since summer 2011, more than 6,000 of these brackets have been in use for the expansion of the Panama Canal. With the robust and flexible bracket system, the loads from the fresh concrete pressure are transferred without formwork ties via the bracket into the climbing anchors.Typical areas of application include dams, locks, cooling towers, bunkers and vaults, pier heads and tunnels.
The new climbing system SCS is characterized by its high level of cost-effectiveness because, thanks to the modular design concept with its multi-part brackets, it can be optimally adapted to the respective requirements and building geometries. Moreover, the high load-bearing capacity of the brackets together with high utilization grade of the certified anchoring makes the new system more efficient than the SKS bracket it has replaced. For the starter and for all subsequent standard cycles, the same formwork and the same system components are used. In order to be able to work safely on forward and reverse-inclined structures, the finishing and concreting platforms can be tilted by 15° and 30°, whilst the working platform can be adjusted continuously. As a result, it is always be aligned horizontally thus providing a safe working environment.
PERI presented the system in two versions. The SCS 190 bracket is available as a low-cost option that requires very little space. For striking, the formwork is simply tilted. With the SCS 250, the formwork can be retracted by more than 60 cm by means of a carriage. This provides sufficient space for all formworking and reinforcement operations.
LPS Screen: the lightweight climbing protection panel
PERI developed the new LPS Screen (LPS = Light Protection System) climbing protection panel as a weight-optimized alternative to the conventional, closed enclosures. The rail-mounted protection panel with rentable mesh panels as the enclosure can be used extremely flexibly and is easily adapted to suit complex building forms thanks to the telescopic function. The close-meshed panels serve as a wind deflector as well as providing anti-fall protection during assembly of the top slab formwork. One particular advantage during striking of the respective floors is that the light-transmissive structure of the mesh panels allows working operations to be carried out in daylight. In addition, the panels are very light which simplifies installation and the climbing procedure whilst also reducing the load on the building itself. The meshed enclosure is quickly and easily mounted to the LPS climbing rails by means of clamp connectors – a crane is not required. Continuous connections are possible thus allowing a free arrangement of the climbing rails.
The slab shoe-guided climbing rails facilitate a fast and safe moving procedure. As an option, mobile hydraulic climbing devices also allow crane-independent moving.
PERI offers the LPS Screen in two versions. On the one hand, straight and continuous and, on the other, with a working platform that provides access to the stopend formwork.
The mesh panels can also be used with RCS climbing rails whereby they are simply clamped to the climbing rail with the same LPS clamp adapters. With this lightweight and completely rentable solution, the proven PERI RCS P climbing protection panel is even more cost-effective.
The RCS MP Landing Platform: fast moving procedure with flexible landing platforms
For moving formwork and construction materials in high-rise buildings, PERI presented the RCS MP landing platform at bauma 2013. Optionally, the new system can be either anchored in the slab or simply clamped in position between two storey slabs by means of MULTIPROP props. The RCS MP landing platform is supplemented through the checker plate decking and LPS mesh enclosure. The solution is completely rentable and is delivered already pre-assembled. The platform has a cantilever of 3.75 m and serves to move the SKYDECK and building materials whereby the 5.50 m cantilevered platform is used for moving large-sized slab tables. With the larger version, post tensioning is integrated in the side protection which minimizes the amount of deflection on the platform.
PERI Civil Engineering Technology
For tunnel and bridge construction, a number of new systems have been developed over the past three years which have already impressively proved themselves during tough jobsite conditions. Shortly after being showcased at the last bauma, the VARIOKIT heavy-duty shoring tower, for example, was successfully used in summer 2010 as shoring for bridge construction as well as for supporting extremely heavy precast concrete elements. And the new VARIOKIT balanced cantilever equipment was used for the first time in spring 2011 in Poland for the construction of a bridge over the River Dunajec.
PERI presented all of the new solutions in April 2013 in the Civil Engineering Technology area of the stand with a number of exhibits, but also especially through demonstrations and competent presentations of solutions by the PERI team of experts. In addition, PERI also dedicated one particular area to the design and realization of complex forms. PERI´s special expertise ranges from planning and cutting-to-size through to the creation of 3D formwork units which can be assembled on the construction site similar to a system formwork.
The VARIOKIT heavy-duty truss girder
PERI has clearly expanded the application possibilities of the VARIOKIT engineering construction kit. With new VARIOKIT system components, it is now possible to also create a heavy-duty truss girder – as a suitable further development to supplement the VARIOKIT heavy-duty shoring tower. During the development, PERI took into account the load-bearing capacity of the tower as well as the challenging requirements of everyday construction work. At bauma 2013, the heavy-duty truss girder was impressively presented having been positioned under a bridge with original dimensions.
The modular lattice system can be used for spans up to 40 m and is characterized by a very high load-bearing capacity. With the continuously adjustable telescopic support frame, all spans can be realized with centimetre precision. In addition, the calotte bearing allows easy adaption to the longitudinal and lateral inclinations of the superstructure. The heavy-duty truss girder can be quickly assembled by means of fitting pins.
The compatibility with the VARIOKIT heavy-duty shoring tower through the VRB main beam, facilitates optimized solutions in the heavy-duty shoring sector, whilst the optional PERI UP scaffolding in the bottom section provides completely safe working conditions.
The VARIOKIT balanced cantilever equipment
The VARIOKIT construction kit has been used very successfully in recent months also for bridge structures with different superstructure cross-sections. With new components for the longitudinal direction of the balanced cantilever equipment, up to 5.75 m long segments can be concreted. In the transverse direction, existing system components are used. Thus, PERI achieves a maximum level of adaptability for a wide range of bridge sections. Furthermore, the moving procedure to the next concreting section is now extremely practice-oriented. Then, thanks to a newly developed mechanical solution, the required manual work is quickly carried out.
As all system components, with the exception of the tie technology, are available in the PERI rental parks, the balanced cantilever unit is also extremely cost-effective with VARIOKIT. All modules incidentally can be re-used for future projects without requiring any further adaptation – the majority even for other types of civil engineering structures.
The new VGK-2 parapet bracket
For shuttering of bridge cantilevered parapets and for their refurbishment, PERI presented new parapet brackets. These are characterized by a low individual component weight of a maximum 22 kg and a high degree of flexibility for adapting to different parapet geometries. Because the brackets can be mounted and aligned while positioned on the platform, this improves work safety. The completely enclosed decking, side protection as well as anchoring with general building inspectorate approval guarantees safe utilization. The bracket makes a very convincing and impressive case during refurbishment work: firstly, as a working area for dismantling operations and subsequently as the basis for the formwork of the new cantilevered parapet.
PERI UP Scaffold Technology
PERI presented a wide range of scaffolding solutions and applications through numerous demonstrations on the market square area and a number of dedicated demonstration areas. Safer and faster assembly and dismantling along with access means for different requirements was the main focus throughout. New system components were presented for use in industry and also for the weather protection roof LGS.
New: the PERI UP Trolley UFS 20
This newly-developed trolley serves to create rollable suspended scaffolding on steel girders. It is intended for hanging scaffolds which are mounted, for example, on the underside of oil platforms or for bridges on I-shaped steel profiles. The trolley is suitable for flange widths from 200 mm to 320 mm and flange thicknesses up to approx. 40 mm. The rollers are bearing-mounted and allow connections to inclined girders up to an angle of 15°.
The system spacings of the scaffold are retained during use of the UFS 20 trolley in spite of variable distances between the steel girders: as the position of the standards vis-á-vis the girder axis can be continuously adjusted up to 125 mm, this always results in system dimensions in 25 cm increments for the scaffold sub-structure.
Improved working safety with the weather protection roof LGS
The LGS lattice girder system has established itself as a reliable and easy-to-use lightweight weather protection roof – supplemented by components for the support and ridge formation. For closing the frame construction with sheeting, PERI has now developed a considerably faster solution. In addition, the new brackets ensure that working conditions on the roof are much safer.
Closing the construction with sheeting is now much easier and faster because the optimized Keder tracks along with the new Keder couplings reduce friction and thus the amount of physical effort required. In addition, a new eave element with a curved shape allows the sheeting to be pulled more easily together and tightly closed also in the support areas of the protection roof. Another new feature is that through the integrated smooth-running mechanism, the sheeting can be evenly pulled across the complete width on rollers.Through this new solution for the installation of the sheeting, transport of the Keder sheeting is also simplified.
Furthermore, PERI has developed new system components that ensure safe access to the protection roof. Then, in order to detach prefabricated roof trusses from the crane or brace individual pre-assembled truss sections with ledgers and diagonals, access means within the construction is absolutely necessary.
The new brackets are mounted on the LGS element with 3.00 m spacings, whilst safe walkways along the truss girder are formed with proven UDI decks and standard guardrails. When working under the roof, the use of personal protection gear against falling is therefore not necessary. The pre-assembly of the brackets is carried out together with the roof segments on the ground – to a very large extent without tools. Then the complete units are lifted by crane into the required position. Access is possible through the load-carrying system and support construction.
Quickly mounted – the new ULS Flex lattice girder
Comprised of lightweight individual components, the steel ULS Flex lattice girder is primarily intended for those applications where the long length of single-piece lattice girders means installation cannot take place.
The girder consists of five lightweight individual components with a maximum length of 1.50 m and a top weight of 15.4 kg. The quick and easy assembly with pins and cotter pins – without any tube coupling connections – makes the new lattice girder extremely practical for every construction site. Due to its compact dimensions and low individual weights, the ULS Flex system parts fit through narrow manholes and small freight elevators - an important aspect, for example, during renovation work in old buildings. The easy to handle elements facilitate optimum adaptation in increments of 25 cm for bridging lengths from 3.00 m to 9.00 m.