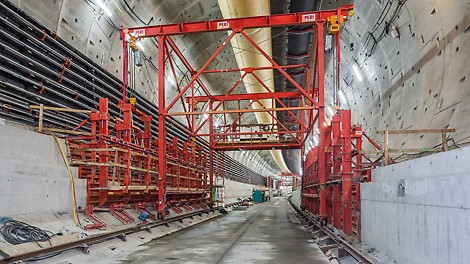
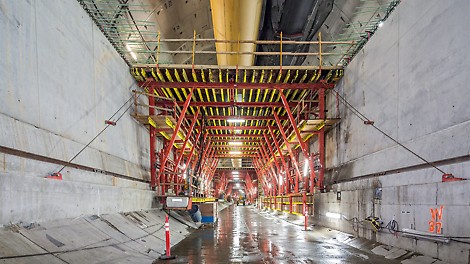
##press.download.headline##
##press.media.headline##
After the Alaskan Way Viaduct had suffered considerable damage due to a major earthquake in 2001, initial preparations were made for a replacement. Eight years later, plans for a bored-tunnel emerged. In 2011, Seattle Tunnel Partners (STP) was awarded the contract for the planning as well as construction of the tunnel – a joint venture of the Tutor Perini Corporation from California and Dragados USA.
Bertha, one of the world's largest tunnel boring machines (TBM) excavates a tunnel with a diameter of around 17.50 m which is then directly covered with 60-cm thick precast concrete ring segments. Inside the tube, a double-storey carriageway is realized. The required walls as well as the supported tunnel slab are being formed by means of mobile formwork solutions from PERI.
The requirement: mobile formwork carriage on rails
The task for PERI engineers was to develop mobile formwork solutions in order to efficiently shutter and concrete the reinforced concrete construction within the circular tunnel tube, and to move the carriage to the next section. Execution is divided into three construction phases namely corbels, side walls and slabs which subsequently forms the upper carriageway. There are also cast-in-place walls above the elevated slab formed with PERI DOMINO.
For the planning, the PERI team had to take into consideration a wide range of boundary conditions which included the numerous tunnel curves as well as the required lateral inclinations of the slabs. As all TBM formwork carriages are designed to be moved along one and the same rail construction through the entire tunnel, specific planning of the concreting sections was particularly important for ensuring efficient implementation. Logistics also had to be taken into account: because the TBM has to be constantly supplied with materials such as the concrete ring segments, the overall concept had to include a sufficiently large passageway. The formwork carriages were eventually designed to accommodate 16.45 m long sections – based on the expected average drilling rate of the tunnel boring machine.
The execution solution
Initially, the construction team levelled the floor of the tunnel with a layer of concrete on which rails were installed for moving the corbel formwork carriage. In addition, a flat working surface was created for the starting unit that forms the foundation of the entire construction.
The first carriage directly following the TBM carries the side formwork of the starting unit – one formwork set per tunnel side. The corbel formwork was custom steel formwork. MAXIMO came in after to form the walls. Rails for the wall and slab travellers are on top of the corbel.
On the one hand, the starting unit forms the foundation for the rising side walls of the inner tunnel. On the other, it also subsequently serves as a support for the prefabricated panels that are installed as the bottom carriageway slab after the in-situ concrete work has been finally completed.
After the foundations have reached the required minimum strength, the 4.50 m high side walls of the inner tunnel are concreted directly on the starters. For this purpose, two formwork sets consisting of MAXIMO Panel Formwork are used which are moved from concreting section to concreting section on a second formwork carriage. While one set of formwork remains in the rear tunnel section after the concrete has been placed, the second formwork set is reassembled further ahead in the tunnel after striking.
In the third construction phase, a slab is constructed that subsequently forms the carriageway which will carry southbound traffic. The bottom slab is realized with a total of six slab formwork carriages using the back-step construction method: three slightly longer carriages with project-specific formwork on the basis of VARIOKIT Steel Walers and GT 24 Formwork Girders serve to carry out concreting in advance for the slab sections. The resulting interstitial spaces are subsequently closed by means of three slightly shorter slab formwork carriages.
Well thought-out, economical overall concept
Through the close cooperation of all parties involved along with early planning, a coherent overall concept for allowing efficient construction of this complex structure was developed and implemented. Due to the fact that most of the system components used have been supplied from the PERI rental park, the formwork solution has also been very cost-effective. In particular, the use of system components from the VARIOKIT Engineering Construction Kit has enabled the construction team to meet the strict schedules for all formwork operations as well as the required geometrical adaptations in spite of the less-than-favourable conditions. In addition, the use of hydraulic solutions for shuttering and striking in certain areas facilitated faster working. The travelers also are advanced hydraulically.